On November 7 and 8, 2024, the International Engineering Program (IEP) reprised its role of biennial host to the Annual Colloquium on International Engineering Education (ACIEE). This year marked the first time that the ACIEE has been hosted by the IEP back on URI’s Kingston Campus since the inaugural symposium created by URI German professor John Grandin 27 years prior. It was also the first event of its kind that the IEP was able to host in person since 2018 – making this particular iteration of the conference a very special occasion to network and learn from others in the fields of engineering, languages, study abroad, intercultural competence and industry.
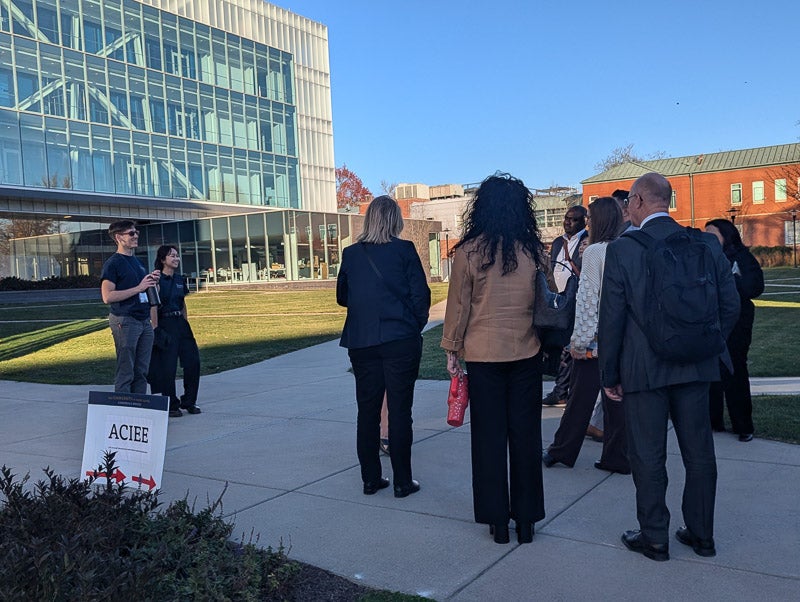
Attendees, presenters, moderators and keynote speakers came to campus or Zoomed in from around the state, the country and the world, in order to participate in this unique forum of global engineering topics. The two full days of activities included: three keynotes, four specialized workshops/panels, 14 concurrent sessions with a total of 44 presentations on a variety of relevant themes, time to network over lunches and coffee, tours of the URI campus and of the Fascitelli Center for Advanced Engineering, as well as closing poster showcase with cocktail reception. Additionally, participants had the opportunity to dine together at the Matunuck Oyster Bar, a local restaurant owned and operated by URI alumnus Perry Raso (that received rave reviews on the ACIEE’s post-event survey!), and to join in for an optional tour of Newport following the conclusion of the conference.
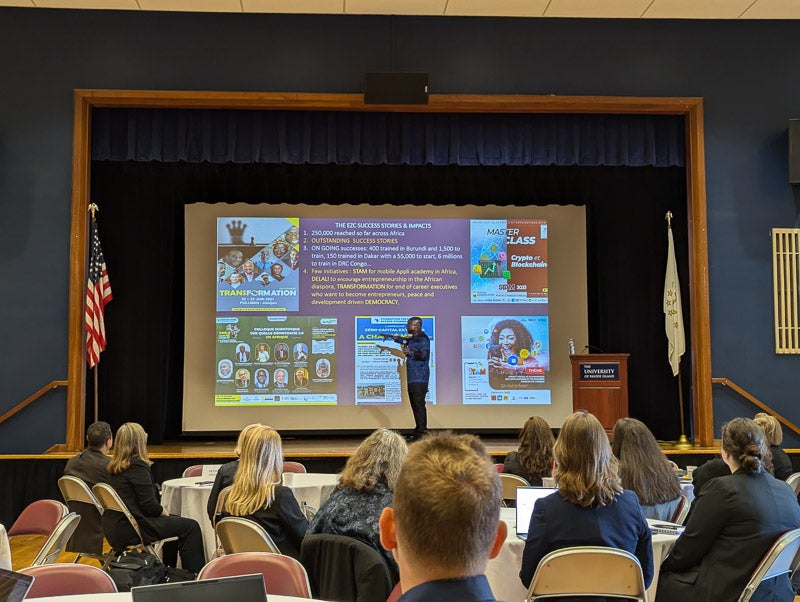
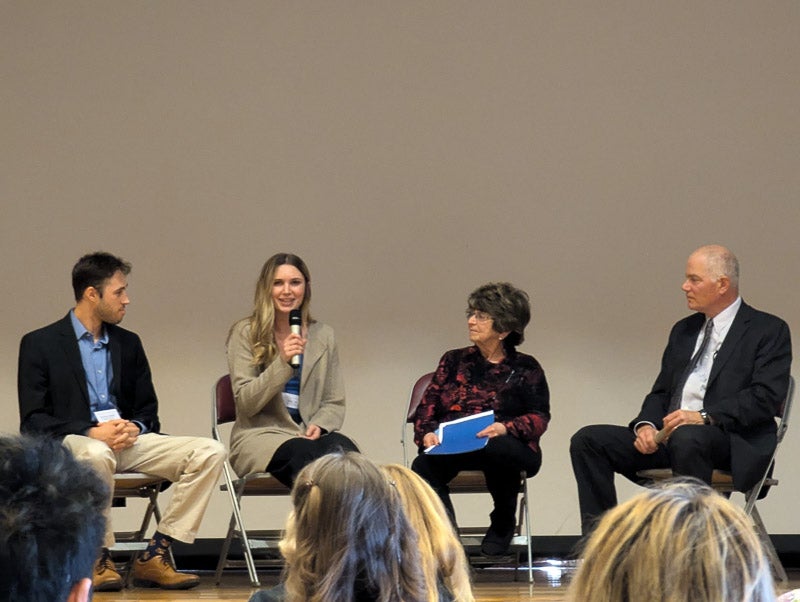
The three ACIEE keynote speakers represented the fields of engineering, entrepreneurship and language policy. Samuel Mathey, president and founder of African Foundation for. Entrepreneurship and Economic Development, an non-governmental organization that advocates for the cause of entrepreneurship in Africa, kicked off this year’s colloquium with his energetic and empowering presentation, entitled “Developing Entrepreneurs in Funding Constrained Africa: the Zero Capital Approach”, by having people think more deeply about how businesses can be launched without the capital traditionally required. Over lunch on day one, Michael Nugent, former Language Flagship and National Security Education Program director, spoke about the topic “Building Effective Communities of Change: Reflections on Shaping Policy to Transform Language & Cultural Education Across Regions & Disciplines”. URI/IEP alumni Zachary Smith, ELE/German & Chinese `20, and Keara Cole, CPE & Chinese `20 and recipient of the prestigious Boren award, joined in for the Q&A panel following the main segment of the keynote, adding an extra layer of depth and relevance to the conversation. On the following day, Meghan Soens, a biomedical engineering/Spanish IEP ’07 alumna, IEP board member and vice president of sales at Boston Scientific, drew the audience into her talk, “Medical Device Innovation: The Role of Medical Device Sales and Marketing in Driving Change in Healthcare”, by interweaving her own career journey; from developing patents to a leadership position in sales into each point she made, and showing how the IEP set her up for her success.

The featured workshops, hosted by speakers from a variety of universities, spanned the topics of intercultural competence and diversity, grant funding for international education research, and building and sustaining international programs like the IEP. Meanwhile, the special panel on innovation and entrepreneurship incorporated perspectives from those in both industry and academia in order to tackle big ideas and new trends through public-private partnerships.
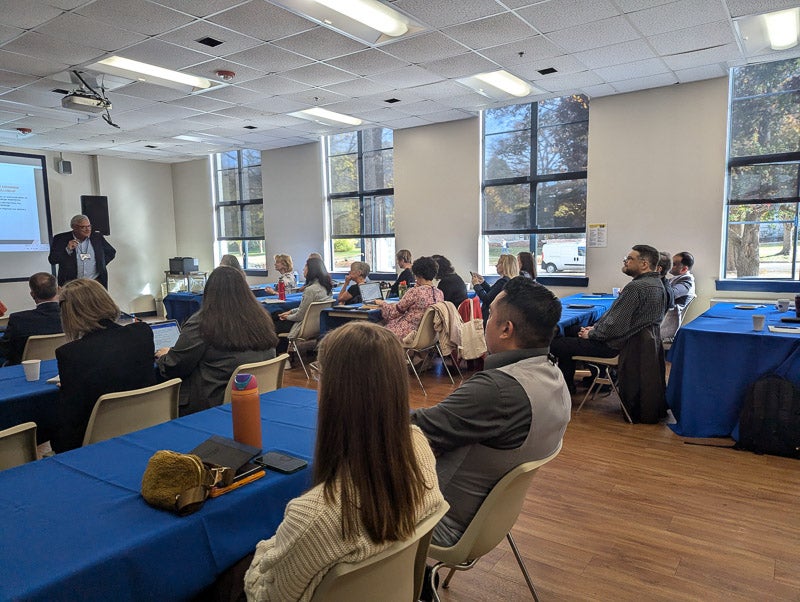
Counted among the honored guests of this event were URI President Marc Parlange and Anthony Marchese, Dean of the College of Engineering, joining the IEP for the ACIEE’s closing ceremony on November 8. During this final activity, where students, attendees and presenters had ample time to ask questions and make new connections, it was also announced that the next ACIEE will be held in 2025 by Texas A&M University. To learn more about ACIEE 2025, click here.
This event was sponsored by the DAAD German Academic Exchange Service and URI’s Colleges of Engineering and Arts and Sciences.