With support from the National Science Foundation, a multidisciplinary collaboration that includes GSO associate professor Melissa Omand is working to bring biodegradable plastics to the ocean, and to market.
By Hugh Markey
When Associate Professor Melissa Omand came to GSO in 2015, collecting data on ocean currents meant deploying large numbers of instruments. It also meant that most of those instruments would never be retrieved and would be left to drift in the currents. “They’re typically not picked up at the end of the deployment because it’s cost prohibitive and, logistically, nearly impossible to go out and recover every single unit after they’ve been drifting for weeks or months or years.…I started to build tools that I felt were missing,” said Omand.
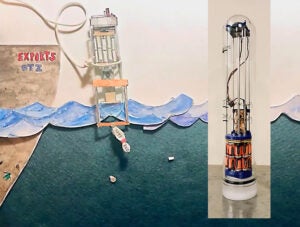
Omand developed a subsurface float that was low cost and designed to be expendable. Doing so prompted her to consider the implications of putting large numbers of disposable instruments into the ocean and what could be done about the waste created through those deployments. “That was the beginning for me of thinking about how to make these instruments and sensors less harmful to the ocean,” said Omand. With this concern, she approached Alyson Santoro, a microbiologist and associate professor at the University of California Santa Barbara about building inexpensive floats that could be completely biodegradable. Today, Omand and her colleagues at Nereid Biomaterials are developing biopolymers that essentially combine bacteria with a plastic material that is consumed by the bacteria and dissolves, leaving no plastic behind.
Initial Steps
Investigations began with Polylactic acid (PLA), a thermoplastic monomer derived from renewable, organic sources, which some had claimed was biodegradable. However, studies suggested that PLA was as non-biodegradable in the ocean as other petro-based plastics, and could persist for hundreds of years. Omand and her colleagues thought “Well, how can we improve this?” As a microbiologist, Santoro investigated why PLA wasn’t sufficiently biodegradable and considered adding various microbes from the ocean that might be needed. “Santoro questioned why the microbes were not eating PLA—perhaps the cause was that the material was missing some nutrient or enzyme.”
Eventually, the researchers mixed microbes directly into PLA, which would be activated at the end of the instrument’s life. For Omand, this was an ah-ha moment: “Oh, this would be so cool! My floats would basically eat themselves at the end of the experiment.”
The core team expanded as Anne Meyer, a synthetic biologist at the University of Rochester, joined a geogaphically dispersed group. Anne had done some of the first 3D printing with living materials and has worked on projects like self-healing concrete and applications that use bio-inks composed of bacteria.
Finally, the researchers met with chief technology officer Alison Pieja at Mango Materials—a company that specializes in sustainable materials. Mango Materials was using a novel approach to producing a biopolymer—Polyhydroxybutyrate (PHB)—from bacteria that use methane as a food source. Moreover, the companyy had shown that PHB degrades much faster than PLA in realistic/true ocean environments (deep, cold and colonized by marine microbes). With much of plastic’s desirable properties, PHB biodegrades in a fraction of the time. Given the obvious synergies, Mango Materials joined the team.
Working it Through With the NSF
The multidisciplinary talent now assembled at Nereid Biomaterials and the potential for sustainable environmental benefits, made this project a good fit for the National Science Foundation’s (NSF) Convergence Accelerator program, which “speeds use-inspired research into practice through a two-phase process.” The team thought, if they were right, then maybe the technology would have commercial value beyond its own purpose-built applications, like ocean instrumentation.
Omand imagined getting funded would be a heavy lift. “First, it’s a little bit outside of our lanes in terms of research. Second, this wasn’t a pure research question so much as an applied research question.”
On the other hand, “The new directorate from NSF is much more focused on applied solutions and technology transfer,” observed Omand. “So essentially, I think it’s a very bipartisan intent to support applications of knowledge to products that can be commercialized.” Nereid Biomaterials was invited into the program.
Phase One of the program, “Team convergence and proof-of-concept development,” prescribed four key objectives:
- Participate in an accelerated nine-month planning effort.
- Apply a multidisciplinary approach while progressing toward proof of concept, identifying new team members and partners along the way.
- Learn and apply fundamentals through a hands-on innovation curriculum.
- Cooperate in a competitive environment—sharing expertise and resources—to stimulate ideas and identify skills, expertise and partnerships needed for progress.
During its first year, Nereid Biomaterials conducted customer discovery, “trying to really isolate what the problem is and make sure we are addressing a real need and not just a perceived need, or not just our own needs,” said Omand. “In the last six months we’ve made a lot of progress.” Potential customers were polled. “We couldn’t tell them much about exactly what our product was. [The NSF] really discouraged trying to pitch a product, but rather try to understand customers’ needs, then make a prototype that addressed those needs.”
According to the NSF, at the end of phase two, “Prototyping and Sustainability Planning,” “…teams are expected to provide deliverables that impact societal needs at scale and are sustainable beyond NSF support.” Teams continue developing solutions over two years through a cooperative agreement and are awarded up to $5 million. They also apply fundamentals developed in phase one and participate in an entrepreneurial curriculum, including “product development, intellectual property, financial resources, sustainability planning, and communications and outreach.”
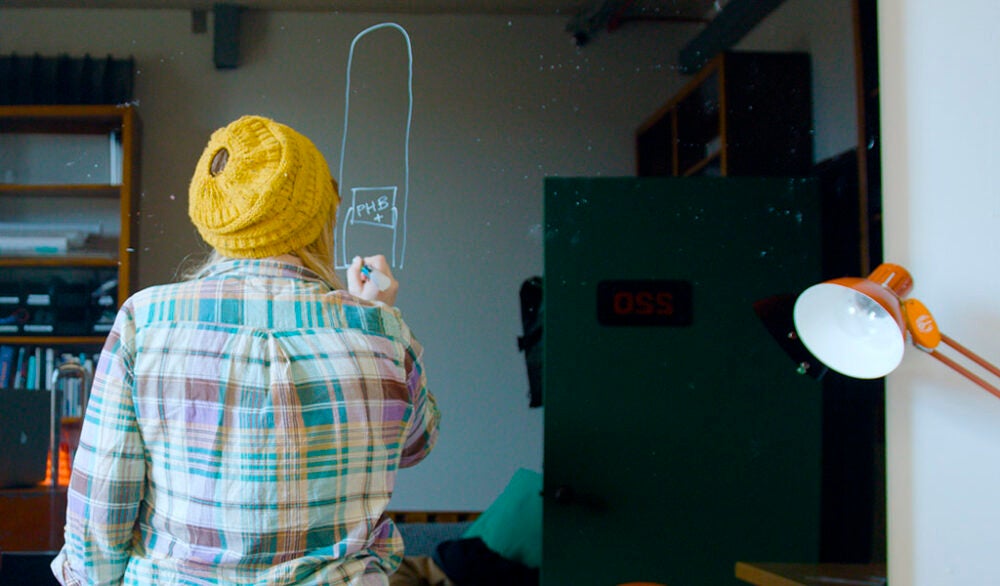
Grappling With Reality
The leap from phase one to phase two came with challenges, according to Omand. “We had to do ‘Shark Tank’ style pitches. It was one of the biggest proposals I’ve ever put together, for sure. We knew from the beginning the competition was going to be steep. The expectations for this award are very different from other kinds of awards I’ve been involved in.” In fall 2022, Nereid Biomaterials won the nod from the NSF to proceed to phase two.
Phase two also comes with a wealth of education and training. “There’s a lot more engagement. We meet with coaches regularly; we’re getting lots of feedback. All in hopes the support, the training, will accelerate and improve our chances of successfully launching a sustainable startup.”
In phase two, the team must prove their product will actually work by conducting rapid testing of ideas to create a minimum viable prototype. “You might test tangible things, or concepts. We’re iterating to find the best product-to-market fit. We are working with our first invested customers, and we’ve already delivered some of the material.”
NOAA’s Pacific Marine Environmental Laboratory (PMEL) is one of these customers. PMEL is building injection-molded “dog bones” to stress test moorings. Meanwhile, Metocean will use the material to build a type of drifter that tracks microplastics in the ocean. “They really want a drifter that’s not made out of harmful plastic,” says Omand.
Customers, especially science-oriented ones, need to know the material they’re using is truly biodegradable. Nereid Biomaterials is investigating their materials’ capacity for degradation. “We’re quantifying degradation rates, because one of the needs was actual data,” said Omand. “There’s a lot of products out there that purport to be biodegradable or not harmful for ocean environments, but there’s no evidence or data to back that up.”
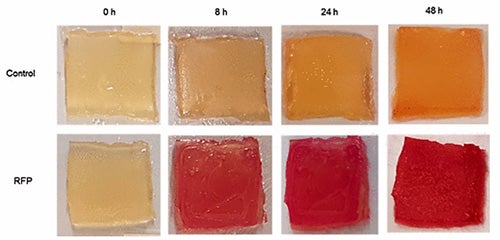
“We’re also doing toxicity tests to make sure what we do is not harmful in some unintended way. We’re doing material characterizations, so we can report properties like strength or toughness. We’re looking at shelf life. We’re actually putting materials out in the ocean to record what happens over time.”
Nereid Biomaterials is now prototyping different products. For example, 3D printing with bio-ink can mesh microbes with the material directly, or bacterial spores are being embedded. They’ve found that bacteria under stress form shells, which are very robust to high temperature or desiccation. “We think we can blend them in with our PHB,” says Omand. “It would be a mixture of bacteria and PHB that might be activated upon contact with seawater.”
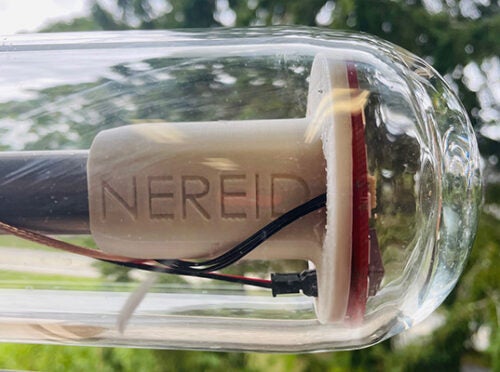
What Lies Ahead
At $5 million, the phase two award is the largest Omand has helped win. “It means we can continue this exciting work. The schedule is highly compressed and we’re motivated to get this work done within the timeframe of the award. The pace has required us to be very coordinated between the institutions and to have a lot of communication. We’ve hired a program manager that’s helping everybody keep on top of things.”
As entrepreneurs, the principal investigators at Nereid Biomaterials are preparing to fundraise more broadly to continue beyond phase two. “Right now the venture consists of an already existing company and three academics, women in their mid-careers. We’re figuring out whether we’re ready for what might come next and what our level of commitment is to become.”
Will someone be a CEO or CTO of a startup, rather than an associate professor? Is it feasible to do both? The future for each individual is yet to be determined. “It’s common to remain on a board as a technical advisor, for example. And it’s possible to take on a leadership position. I’m not opposed to that idea at all. The advice we’ve received is that a phase two award changes our lives. It changes the whole trajectory of what we do. I’m pretty happy about it so far.”